


Apec
About company
As a manufacturer of both the equipment and control systems, APEC offers a comprehensive system to meet all your process needs. This approach allows us to address your entire program and deliver solutions that will result in precise control of the proportioning of your recipe ingredients with reduced cost.
Our one source approach offers:
- A large product line enabling our in-house engineers to design and assemble complete systems.
- The ability to customize equipment and systems you require to meet your specific manufacturing needs, as opposed to an “off the rack” answer.
- A corporate culture that promotes continual innovation and the introduction of new products to improve your operations.
Company News
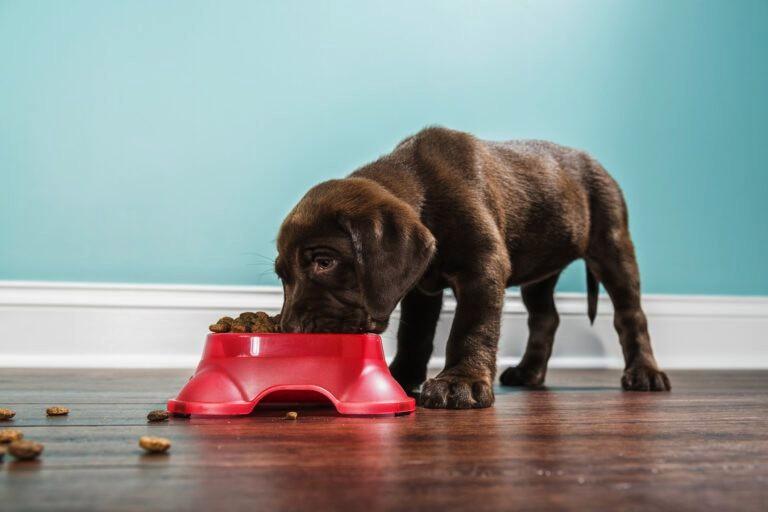

4+ MIN





07/06/2023
5 Essential Pet Food Manufacturing Equipment Types
Being able to reliably, affordably and easily feed our pets has been an important part of our ongoing relationships with our pets. In the modern industrial era, several types of pet food manufacturing equipment have played a key role in widely distributing pet food. Let's take a closer look at the essential pet food manufacturing equipment supporting the pet food industry today. 5 Essential Pet Food Manufacturing Equipment Types Today, there are many different types of pet food. This includes a wide range of pet types, from fish to birds to rodents to cats and dogs and many more, as well as many different types of food, including wet food, dry food, canned food, fresh food, and more. Different types of pet food utilize many different ingredients, processes and pet food manufacturing equipment. In this blog post we'll take a look at a few of the most essential processes. A startling 25% of Americans added a pet to their home in 2020. This was an especially difficult year, indicating that many of us rely on our pets for companionship and comfort. During this time, US pet food sales rose 10%, with e-commerce sales rising sharply. Increasingly, pet owners are seeing their pets as family members, which can have numerous benefits, mostly linked to reduced stress and loneliness. With bonds between people and pets growing stronger, an increasing number of pet owners are looking for high-quality and speciality pet foods, including wet food and refrigerated food. However, dry pet food like kibble still remains the dominant type, accounting for 57% of pet food sales. Since cats and dogs are still by far the most popular type of pet, we'll mainly discuss the essential pet food manufacturing equipment for dry dog and cat food. Mixers Industrial mixing is one of the most important types of food processing equipment, including pet food. Large-scale mixers make it possible to mix ingredients quickly, efficiently, and uniformly, processing 5, 10, even 15 tons of material at one time. These mixers are also capable of working with a wide range of materials, including very fine powders to thick liquids and tough solids. For pet food processing, mixers can be important at several points, from mixing cornmeal and other grains to oils and fats, meat-based products, and more. Without large-scale pet food mixers, it would be difficult to process the amount of food we would need to reliably and affordably feed our pets. Extruders Extruders push mixed material, usually a dough or a paste, through a metal die to create uniform pieces. Extruders are important pet food processing equipment because they make it easy to create food that is easy to package, ship, and store. Extruders also create nutritionally uniform pellets, removing the guesswork in balancing protein, fats, carbohydrates, vitamins and minerals. In addition, these pellets are easy to work with, so they can be easily coated with flavorings and fats. Spray Coating Adding fats and flavorings to kibble is important for making the food palatable for pets, but it's also important to ensure that the pets get the right amount of fats, vitamins and minerals in their diet. Spray coating makes it easy to add liquid coatings to pellets. This process is both fast and efficient, so the pellets can move through the process quickly and get to packaging and then on to the customer and their pet. Mist Coating Mist coating takes liquid coating one step further, making it even easier and faster to apply liquid coatings to pellets. Mist coating equipment uses an atomizing system which turns liquid coatings into a fine mist, which evenly coats the material as it falls through the coating chamber. When comparing liquid coating systems, mist coating is one of the most efficient methods, since it provides more even coating, reduces waste, requires less clean-up, and tends to be gentler on the pellets, decreasing breakage and loss. Track and Tracing Track and tracing systems, which can include a wide range of equipment, are essential to all modern-day food systems, and pet food is no exception. By tracking materials and finished products through each process, and then on to retailers and customers, it's possible to detect where contamination exists, and stop contaminated products before they do more damage. Though other processes are designed to kill bacteria and tests are designed to detect dangerous chemicals, no process is 100% effective. When bacteria or other dangers make their way into pet food, track and trace systems can show where the contamination came from, and pull the contaminated goods from the shelf as quickly as possible. by APEC Source: All Pet Food
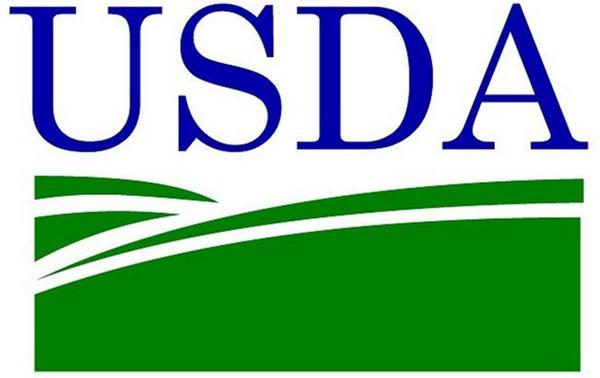

3+ MIN





26/04/2020
USDA Safety and Compliance Requirements for Food Processors
Preventing illness and contamination across the food supply chain is a challenging process, with many regulatory bodies involved. It can be difficult to know where the responsibilities of one group ends and another begins. The USDA and the FDA work closely together in different areas of the food supply chain to ensure sanitation and safety. In some cases, USDA safety and compliance requirements and inspections are similar to the FDA's, and in other ways they are different. Grant of Inspection and HACCP The USDA requires that businesses and facilities working with meat, poultry, eggs and egg products apply for a Grant of Inspection. There are several steps to this process, including application, registration, sanitation requirements, and hazard analysis and critical control points (HACCP), among others. This is similar in some ways to requirements set forth by the Food Safety and Modernization Act (FSMA). HACCP for a Grant of Inspection is similar to FSMA requirements in many ways. HACCP requires the following: Written hazard analysis: Where hazards are likely to occur in the production process and how these can be prevented. A flow chart: A flow chart should describe the steps in the product process, the purpose of each process, and any hazards associated. Written hazard plan: For each product, a written hazard plan should address the associated hazards and how to prevent or mitigate risk. Corrective actions: How to prevent a problem or mitigate risk if a problem occurs. Validation and Verification: Validating that the HACCP plan works and verifying that it continues to work. HACCP Records: How to maintain records to show the HACCP plan is being followed. Sanitation Procedures Businesses and facilities that work with meat and poultry must have strict sanitation procedures in place. This helps to prevent the spread of bacteria and foodborne illness, or limit the damage if contamination occurs. These procedures and requirements are also similar to FSMA. A thorough and effective sanitation plan is one of the best ways to prevent illness and mitigate risks in your facility. Your Sanitation Standard operating procedures should include the following. Keep in mind that all facilities are unique, and this list is not exhaustive. Team responsibilities: who is responsible for sanitation and what their duties include. Disassembly: Machines that are not suitable for clean-in-place procedures must be disassembled. Scrubbing: For sanitary cleaning chemicals to work, debris, grease and oil must first be removed from tools and machines. Facility cleaning: The facility itself, as well as the tools and equipment, should also be cleaned, including floors, walls, and ceilings. Sanitary garments: Garments like gloves, aprons, and other gear should be changed at least daily, or more often if necessary. Verification: A process must be in place to show that these procedures are being conducted properly. Corrective actions: If any cleaning procedures are not followed, corrective actions should be in place to stop production if necessary and prevent the problem from happening again. Recording-keeping: Accurate record-keeping shows when cleaning procedures are being conducted, and by whom. Recall Procedures Even the best sanitation and hazard management procedures don't work 100% of the time. This is where recall procedures come in. Just as FSMA requires recall procedures for other food processors, the USDA requires recall procedures for meat and poultry processors. Recall procedures are intended to reduce the impact of contamination by stopping the distribution of contaminated food. A recall can also be used if contamination is not harmful, but foods have been mislabeled or an excess of harmless ingredients have been used. In meat processing and other food processing, the requirements are similar. You should have the following, though this list is not exhaustive. Recall team: who is required to implement a recall and what are their duties? FSIS office: the contact information for your local Food Safety and Inspection Service office. Hazard evaluation: on what criteria do you decide to conduct a recall? Recall scope: how will you determine where products must be recalled from? Records: how are products traced and how do you store and manage these records? Recall notice: how will you communicate your need for a recall? Recall disposal: how will the recalled products be disposed of? Keeping food and facilities safe requires everyone's participation. With thorough procedures in place, as well as verification and regular assessments to ensure these procedures work, you can reduce risks of fines, complications and recalls. by All Extruded
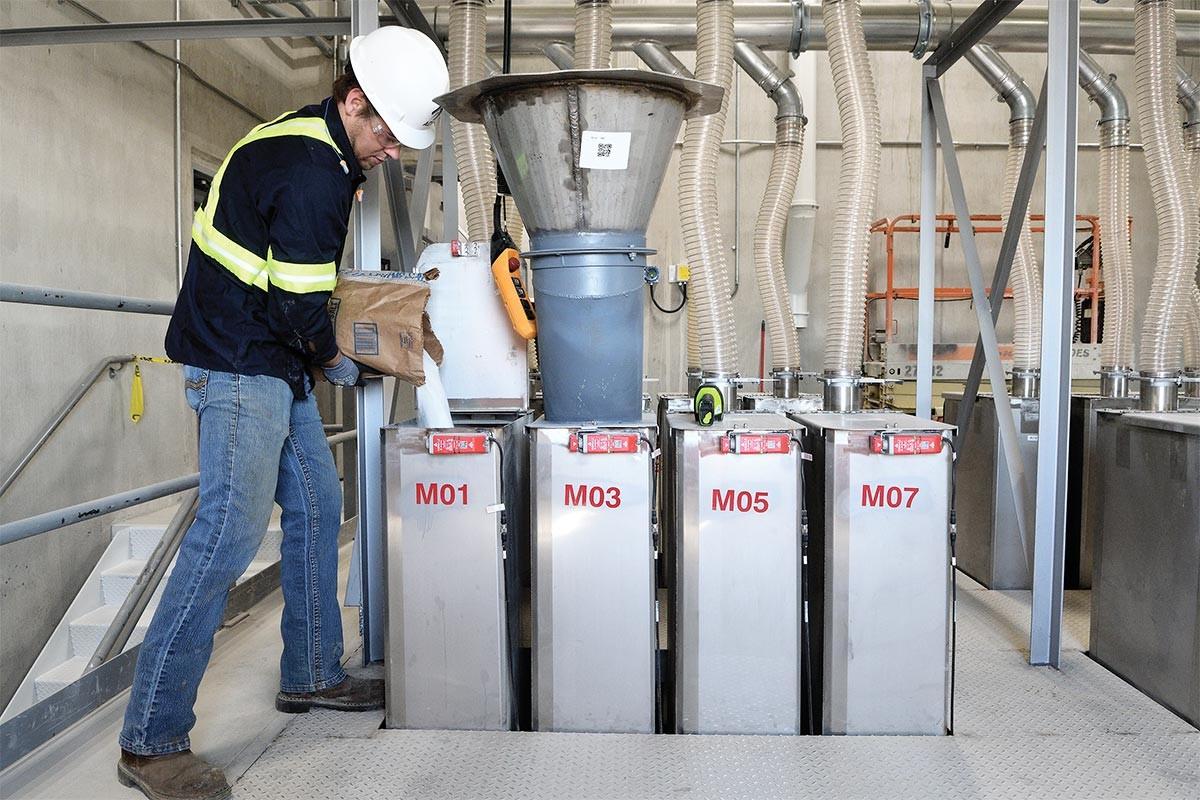

6+ MIN





06/04/2020
Protecting Pet Food ingredients with durable, accurate ingredient handling systems
Many processing applications in the pet food and treat industry can be particularly harsh with high rates of very abrasive products, so equipment must be designed with tougher standards in mind from the ground up. In addition to being durable, equipment must be accurate, easy to clean and efficient to operate, and support food safety. Dave Carney, area sales manager at Bühler Aeroglide, Cary, NC, notes the increased sanitation requirements of today's equipment have driven changes in how they are designed. 'This requires more modularity and ease-of-access to enable customers to adhere to these demands,' he said. Jessica Stank, marketing manager for Lake Odessa, Mich.-based Automated Process Equipment Corporation (APEC), said the biggest trends she is seeing in material handling equipment are related to improvements in the level of efficiency they can provide. '[End users] are looking at ways to automate their process and are looking for equipment that is highly accurate and requires little human intervention to achieve the desired result,' she said. 'Thus, equipment manufacturers are making design improvements to help meet this demand for increased efficiency in processing facilities.' Improvements include specialty components such as capacitive load cell technology on weighing equipment, special bin designs and bulk bag unloaders with massagers or added vibration to assist with product flow. The biggest challenges stem from the types of ingredients used in pet food processing. Stank said certain common dry ingredients are prone to flow issues due to density or other characteristics, and liquids that contain fats and suspended solids can be challenging as well. Tanks that hold fats and oils often heat the liquids. Sensors designed to monitor ingredient levels must withstand harsh environments including a wide range of temperatures. 'Things like stainless steel contact surfaces, equipment that is fully enclosed with locking lids and automation programs that include track and trace technology have addressed concerns regarding safety and sanitation,' she said. Due to Food Safety Modernization Act (FSMA) requirements, pet food processing facilities have moved to food-grade equipment and components that have increased the level of sanitation in plants tremendously. Keeping ingredients contained inside fully enclosed equipment prevents fugitive particles from making their way into the air and onto the floor, which also improves worker safety. Steve Sawyer, factory sales, Dynatrol Division of Automation Products, Inc., Houston, said equipment needs to stand up to the harsh environments found in pet food and treat applications. 'Our customers handle large and small amounts of bulk ingredients and are requesting equipment to operate successfully on products having wider ranges of bulk densities and consistencies,' he said. Sawyer's company manufactures the Dynatrol DJT Level Detectors, which are sensors that provide information on product levels within hoppers, offering high-, intermediate- or low-level detection in temperatures exceeding 300 F. 'We have added a line of specialty coatings for detectors to protect components from steam cleaning and aid in decreasing build-up while not affecting sensitivity,' Sawyer said. This maintains the product's accuracy, decreases down time and increases productivity and product life. Joseph Cross, engineering and process manager, Zeppelin Systems USA, Inc., Odessa, Fla., said producers are demanding increased automation that reduces human interaction to provide labor savings and improves employee engagement by eliminating repetitive tasks. 'This has led Zeppelin to develop our Kokeisl dosing system, a way to dose ingredients in large and small amounts both very quickly and extremely accurately,' Cross said. Equipment manufacturers are challenged to deliver accurate amounts of ingredients quickly. One innovation to address this is a new valve design from Zeppelin.The Kokeisl system offers a unique discharge aid in combination with a large port and a fast-acting discharge valve that can be opened and closed from a 0 to 100% aperture in milliseconds, allowing a large flow of ingredients during the initial delivery followed by a very small trickle-feed to complete the batch with extreme accuracy and repeatability. 'By automating an increasing number of ingredients, many processes may be completed simultaneously, reducing the overall batching time and increasing the throughput of the line,' Cross said. 'Furthermore, increased automation allows for more accurate lot tracking of all major and minor ingredients, allowing for better inventory control and decreased reaction time in the rare case of recalls.' Batching systems Don Goshert, vice president and general manager, Sterling Systems & Controls, Inc., Sterling, Ill., noted the latest trends he is seeing are automatic and semi-automatic minor ingredient weighing/batching systems that dispense raw ingredients while tracking lot information and validating batched ingredient weights. 'Lot tracking with total ingredient material traceability is a requirement in many industries, particularly in the pet food, feed and agriculture, and food industries,' he said. Data collection and management of ingredients and batches from the feed processing batching control system has improved processors' ability to meet product safety requirements. For example, Sterling Systems engineers and produces customized batching control systems that can include as little or as much ingredient lot tracking and traceability as the customer wants to implement. It just depends on the customer's ability to fund and implement the tracking system, as several inventory strategies are available. Utilizing batching controls and automatic dispensing/dosing systems to handle minor ingredients can reduce or eliminate the need for reliance on personnel to manually track or document ingredient lots and weights. Automation streamlining improvements Processors are under pressure to maximize both throughput and accuracy. 'Increasing demand, custom ingredients and pet food quality enhancements have all driven the demand for increasing efficiency in the process controls and automation process systems that produce pet food, such as the minor ingredient batching systems,' Goshert said. The addition of both automation and highly accurate weighing technology can contribute to a major increase in accuracy in a pet food processing facility. 'By replacing a worker with a scoop and a scale with a computer and scale, it virtually eliminates the cost of human error,' Stank said. 'The addition of highly accurate load cells into the ingredient handling portion of the process ensures that costly ingredients are not wasted, and that the recipe is followed to the exact specifications time after time.' A mistake many pet food and feed processing plants make is attempting to justify the automation of all ingredients. Goshert said most successful operations justify ingredient batching automation by applying the 80/20 rule, as the quantity of ingredients is important, but the frequency of an ingredient's use also needs to be considered. 'If you use small doses of an ingredient in almost every formula, that ingredient may be a good candidate for automation too,' he said. When automatic systems are combined with semi-automatic ingredient processing — adding some ingredients by hand when instructed by the control system — justification can be achieved, Goshert added. Cross said equipment providers have been pushed by end users 'like never before' to provide systems that guarantee employee and food safety. 'Increasing levels of automation translates to reduced human interaction with individual ingredients and potentially hazardous equipment, reducing overall workplace injuries and improving batch accuracy and traceability,' he said. 'Also, as allergen concerns grow across the industry, fast and efficient CIP (clean-in-place) systems and the ability to fully sanitize and certify cleanliness has become more important to guarantee consumer satisfaction as well as product quality.' Heading to the future The need to design and maintain ingredient handling equipment for efficient sanitization is one challenge. Another is the evolution of the ingredients being used and how to convey them. These are both areas in which companies believe more innovation is needed. 'I could foresee being able to monitor surfaces for microbials and alert operators that a cleaning is recommended as a market request,' Carney said. Managing all possible data sources from one primary platform is becoming a priority in the pet food and treat industry. Goshert said integrating preventative maintenance planning software with ingredient batching and process controls is an important improvement. 'The demand for keeping the increasingly sophisticated and automated process systems and equipment running at optimal performance has never been greater,' he said. Localizing access to the preventative maintenance planning software from the shop floor or the corporate office area is key. 'Data tracking on the production floor integrated with ERP (enterprise resource planning) systems is essential to maximize benefits,' Goshert said. 'Processors should be sure to work with equipment and control and automation vendors that are on the forefront of data management and can provide complete data tracking with ERP integration.' Source: ADM & Pet Food Processing